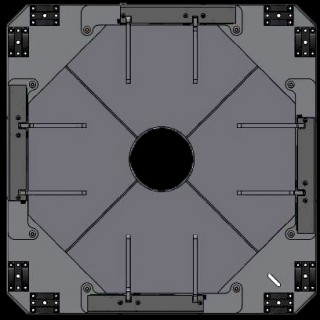
Introduction
Putman Mountain Observatory’s main instrument is a 16” Ritchey Chretien telescope manufactured by RC Optical Systems. The primary mirror is made from Zerodur which is a zero expansion material to make sure the mirror figure and shape do not change by temperature fluctuations.
The primary mirror is also ion milled to 1/40 wave RMS. The primary would be very difficult and expensive to replace if damaged. Because the telescope is often used robotically, the primary mirror must include a mechanism to cover and protect it when not in use.
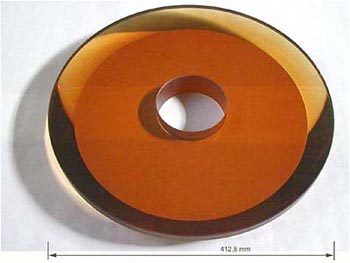
A robotic cover for the primary is necessary to prevent unwanted dust and pollen build up as well as insects such as wasps that may build nests on the primary and damage it. Finally, the robotic mirror cover must have integrated electronics and software to operate the cover remotely and via computer control for automated image acquisition from night to night.
The observatory’s telescope was delivered with a robotic mirror cover from RCOS, however, the RCOS cover utilized machined metal covers that were too heavy for the actuator motors and accordingly, a redesign was in order.
Right Ascension LLC is a company that specializes in designing and building custom mechanical and electronic parts for RC Optical telescopes, among others. Right Ascension even manufactures and repairs control units for the RC Optical telescopes such as the TCC2 and the newer Telescope Interface Module (TIM).
Robotic Mirror Cover Redesign
Right Ascension was consulted about redesigning the existing robotic mirror covers. It was decided that a complete redesign was warranted to improve operation, reliability and better materials. Computer aided design software and techniques were used to create the initial concept and drawings for all of the necessary parts and to insure proper fit and operation. Telescope measurements were double checked and prototype mounting plates were made and fitted to the telescope to test proper fit before committing the design to actual metal parts.
In addition, substantial work was undertaken by Right Ascension to improve the existing TIM control application with software improvements to expose additional COM objects to allow control of the telescope subsystems with scripting control.
Robotic Mirror Cover Description
Right Ascension christened the mirror covers as the Dust Abatement Cover System or DAC System V1.0. The system utilizes a combined four flap layout with each flap controlled by its own DC gear head motor, sensor PCB assembly and wiring harness. Each flap motor assembly is shielded with a polycarbonate cover.
The mechanical parts are machined aluminum and black anodized. Each flap is actuated by an attached 12 volt dc gear head motor. Each flap assembly has a specialized cam design to hold the flap in place at the minimum and maximum swing points of the armature.
Each flap end position is monitored by a sensor and user adjustable. This design allows the user to adjust the fine points of the open and close positions of each flap. The flaps were designed using black G10 fiber board material for exceptional durability. All fixtures are stainless steel and/or brass.
Each flap has a custom designed circuit board containing an indicator led, two industrial grade hall limit switches that are sealed and protected from environmental elements such as moisture, corrosion and dust.
In the image to the right, the circular disks are user-adjustable to fine tune the open and close position for the flaps and indicate to the hall sensors the designated open and close positions.
The PCB on the top of the assembly incorporates a connector cable that is part of the wiring harness to signal to the TIM unit when the flaps are in the open or closed positions.
The 12 volt dc motor is attached to armatures that are connected to the flaps. The motor is also connected to the wiring harness back to the TIM unit.
Installation
The robotic mirror cover came with a concise and illustrated installation and operation manual. Each of the four flaps is a separate assembly. The flaps are designed so that two opposing flaps (3 and 4) close first and the other two opposing flaps (1 and 2) close on top of the flaps already closed.
Flaps 3 and 4 have an edge cut into them which allows flaps 1 and 2 to close into the edge resulting in a uniform, even surface when the flaps are closed. When opened, flaps 1 and 2 open first, followed by flaps 3 and 4. The flaps fit very well when closed, providing a very tight seam impervious to insects.
Each flap assembly is attached to the truss plate with two bolts. The wiring harness is then routed around the optical tube assembly to connect to each flap. Each wiring harness connection is numbered to make sure it connects to the correct flap. The end of the wiring harness is attached to the TIM unit through a parallel DB type interface.
After installation, a new version of the TIM control application was installed on the observatory computer. This is version 2.0 of the TIM control application updating from the older version 1.2. Operation of the mirror covers was tested using the TIM control application version 2.0 running on the observatory computer.
Operation
Despite its design complexity, the robotic mirror cover is very basic in operation. It opens and closes. Whether it does this well is key.
The DAC System met and exceeded all expectations. First of all, the flaps fit very well together, providing a tight seal against dust and insects. In addition, they also fit with precision around the primary light baffle. The fit and finish of the machined metal parts was executed well. The polycarbonate covers for each flap assembly also fit very well with the button head cap screw fasteners. The entire design was well done making sure the four different flaps lined up perfectly once attached to the telescope truss plate. Careful thought was also put into the design to allow user adjustment of the open and close position for each flap. An indicator LED on each flap signals red when opened and green when closed to assist in adjustments. Upon delivery, no adjustment was needed to the DAC System – the flaps closed tight and opened all the way.
The prior RC Optical mirror covers would exhibit some droop or hang due to backlash in the motor gearing which allowed the flaps to hang open slightly depending on where the telescope was parked. The DAC System flaps exhibited none of this droop or hang. Once closed, the flaps closed tight against each other and remained that way despite the position of the telescope.
The flaps open and close within two to three seconds and are significantly quieter in operation than the previous version by RC Optical. The open and close was tested extensively without any failures or mishaps. Prior to deliver, Right Ascension tested the open and close operation hundreds of times without any failures. Open and close operations were also tested with the telescope in many different positions and during slews to the park position. All operations performed admirably.
Improved Software Interface
The TIM is the essential, central intelligence for the telescope, monitoring and controlling various critical subsystems, such as the secondary focuser, secondary heater, primary fans, rotator, and robotic mirror cover. The TIM is also supported by an integrated, ASCOM compliant software system that runs on Windows computers called the TIM control application. This application allows complete control of the telescope via a software interface running on the computer.
The TIM control application provides for standardized ASCOM control of the focuser and rotator. Moreover, the TIM control application exposes a COM object that can be accessed with the Windows Scripting Host in order to control the telescope’s subsystems.
One of the most significant improvements in the DAC System is version 2.0 of the TIM control application. The robotic mirror covers can now be controlled through a scripting interface even when the TIM control application is running and being used by another application to control the focuser, rotator and other telescope subsystems.
For example, a startup script can be written that will invoke the TIM control application, connect to the application, open the mirror covers, turn the primary fans on automatic and then turn the secondary heater on automatic. More elaborate scripts can also be written to include checking the focuser position, home the focuser and then returning to the focuser position after homing. After an automated imaging run, another script can turn off the secondary heater, turn off the fans and then close the robotic mirror cover.
Along with the upgrade to version 2.0 of the TIM control application, Right Ascension provided example VBS scripts to control all of the telescope subsystems through the TIM unit. Using these examples, startup and shutdown scripts were created and performed flawlessly, opening and closing the mirror covers and turning on and off the fans and secondary heater. A sample startup script can be found here: RCOS_Startup_Script
Use the sample script at your own risk. The file extension must be renamed to .vbs from .txt in order for it to run under the windows scripting host.
The implications for automated, unattended imaging are significant. For example, automated imaging software like CCDAutopilot will accept and run external scripts at various points in the automated image acquisition process. Using CCDAutopilot and scripts connecting to the new TIM control application v2.0, the telescope can image objects all night unattended. At the end of the imaging session, the telescope will park, the camera will turn off, the primary fans will turn off, the secondary heater will turn off and the robotic mirror covers will close.
Conclusion
The diagram below depicts how the telescope subsystems interface with the TIM unit and the TIM control application, and from there, the ASCOM and scripting interfaces.
The implementation of the DAC System along with the TIM control application version 2.0 has solved a number of issues and problems. Now the observatory operator will no longer worry about damage to the primary mirror caused by dust, pollen and insects and can rest easy at night knowing the primary mirror will be covered automatically at the end of an imaging session.